You wouldn’t use a dimmer switch to power off a room. And you wouldn’t slam a light switch halfway and call it “brightness control.”
So why do so many engineering teams still confuse globe valves and gate valves?
They’re both linear motion valves. Both use a rising stem. Both are found in power plants, process industries, and pipelines. But if you choose the wrong one for the job, you’ll either waste energy or destroy your valve seals. Sometimes both.
Let’s get clear. And technical.
What Is a Gate Valve?
A gate valve is a fundamental component in fluid isolation. Its flat or wedge-shaped disc moves vertically to either block or allow flow. When fully open, it delivers full-bore, straight-line flow with minimal pressure drop. That makes it ideal where flow must pass freely without resistance.
This is why gate valves are standard in high-pressure steam lines, water distribution mains, and refinery pipelines. At Phoenix Valsteer, these valves are engineered for demanding conditions. We offer them in pressure classes from 150 to 2500, using materials like carbon steel, stainless steel (SS304, SS316), duplex, and super duplex.
What sets our gate valves apart isn’t just the metallurgy. It’s the precision in shutoff and the ability to perform reliably under long-term cycling. Whether you need flanged, socket weld, or butt weld ends—or actuation through handwheel, gearbox, or electric motor—our valves are built to fit real-world operations, not just datasheets.
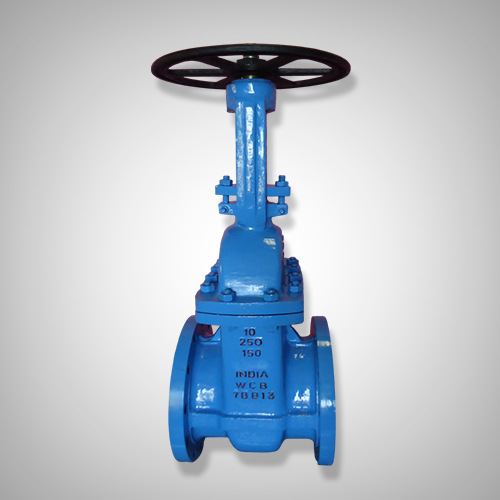
What Is a Globe Valve?
Globe valves are made to regulate flow. Internally, the flow path changes direction, pushing media through a seat and disc that can be finely adjusted. This flow resistance is intentional. It’s what allows for modulation.
If a gate valve acts like a dam—either open or shut—a globe valve functions more like a faucet. It gives you control. Turn it slightly, and you control pressure or volume precisely.
This is why Phoenix Valsteer globe valves are widely used in cooling water loops, feedwater lines, and chemical dosing applications. When flow needs to be managed continuously, these valves deliver.
We manufacture globe valves in Z-pattern, Y-pattern, and angle-type designs. Pressure classes range from 150 to 2500. Materials include SS316, alloy steel, and carbon steel. Actuation options—manual or electric—are configured to match your system demands, not just default specs.

How Flow Paths Differ — And Why That Matters
The most important difference between these valves lies in how they handle flow.
Gate valves offer a straight-through, full-port design. When open, fluid passes through with almost no resistance. That’s perfect for systems where pressure drop must be minimized.
Globe valves introduce directional change. Flow turns, meets resistance, and passes through a narrower seat. This adds pressure drop but gives you control.
If your pipeline needs a simple shutoff and low resistance, go with a gate valve. If it needs modulation, pressure balancing, or responsive adjustment, choose a globe valve
Globe Valve vs Gate Valve: Comparison Table
Feature | Gate Valve | Globe Valve |
Primary Function | Isolation (On/Off) | Flow Control (Modulating) |
Flow Path | Straight-line | Directional change (Z / Angle) |
Pressure Drop | Minimal | Moderate to High |
Throttling Capability | Poor — causes erosion | Excellent — built for modulation |
Sealing Performance | Strong at full close | Excellent, even under partial flow |
Operation Frequency | Infrequent | Frequent |
Best For | Clean fluids, isolation duty | Controlled flow, dosing, pressure control |
Real-World Use Cases
High-Pressure Steam Isolation
Use a forged steel Class 600 or 900 gate valve. When fully open, it minimizes pressure drop while handling extreme temperature.
Cooling Water Modulation
In thermal systems, use a Class 150 globe valve. Adjusting flow helps manage thermal loads and system efficiency.
Chemical Injection
For precise dosing, use a stainless steel globe valve with hardened trim. It provides steady, controllable flow without over-pressurizing downstream components.
Which One Should You Use?
Ask yourself the following:
- Does the media need full flow or full shutoff with little resistance? Choose a gate valve.
- Do you need to adjust the flow regularly or respond to pressure feedback? Use a globe valve.
- Is pressure drop a concern? That points to gate valves.
- Is precise control essential? That’s what globe valves are built for.
Valve Selection with Phoenix Valsteer
At Phoenix Valsteer, we don’t just manufacture valves. We help engineers and plant operators select the right ones—based on the process, the media, and the application.
Our globe and gate valves are available in a full range of materials, pressure classes, sizes, and actuation types. From design to delivery, every valve is built to withstand industrial wear and perform without compromise.
We support EPC contractors, OEMs, and end users in water treatment, power, oil & gas, and process industries.
Need Help Deciding?
Tell us your flow conditions. We’ll help you match the right valve—trim, bonnet, actuation and all.
Explore our valve range or speak directly to a Phoenix Valsteer engineer through our contact page. Your process demands precision. We build valves to deliver it.
Phoenix Valsteer. Flow Control. Engineered Right.