When a valve fails 80 kilometres offshore, it’s not just a leak. It’s production loss, a safety concern, and a logistical nightmare. In oil and gas operations, failure is not an option. That is why Phoenix ValSteer manufactures valves that withstand high pressure, corrosive fluids, abrasive particles, and sour service conditions—without compromise.
Whether you’re handling crude oil, natural gas, drilling mud, or high-temperature steam, our valves are designed to deliver consistent, leak-tight performance across the most demanding environments.
What the Oil and Gas Industry Needs from Its Valves
Common Challenges in Oil and Gas Valve Applications
- High-pressure and high-temperature environments (HPHT)
- Sour service conditions involving hydrogen sulfide (H₂S) and carbon dioxide (CO₂)
- Chloride-induced stress cracking in offshore and subsea applications
- Erosion from solid particles in drilling and separation systems
- Frequent maintenance in remote or hazardous areas
- Strict compliance requirements for safety and environmental protection
Where Our Valves Are Used in Oil and Gas
- Trunnion-mounted ball valves in crude oil export lines
- Duplex gate valves at wellheads and production manifolds
- Super duplex swing check valves on offshore platforms
- Globe valves in refining and hydrocarbon processing units
- Knife gate valves in drilling mud and sand handling systems
Recommended Valve Types and Pressure Classes
Valve Type | Pressure Class Range | Common Materials | Typical Application |
Gate Valve | Class 150 to 2500 | WCB, A105, F316, Duplex | Isolation in flowlines, wellheads, and headers |
Ball Valve | Class 150 to 1500 | A105, CF8M, F51, Super Duplex | On-off control in crude and gas transmission |
Globe Valve | Class 150 to 600 | CF8M, SS316 | Flow regulation in processing and refining systems |
Check Valve | Class 150 to 1500 | CF8M, WCB, Super Duplex | Preventing reverse flow in gas lift and export systems |
Knife Gate Valve | Class 150 to 300 | SS316, Duplex | Handling of drilling fluids, mud, and slurry discharge |
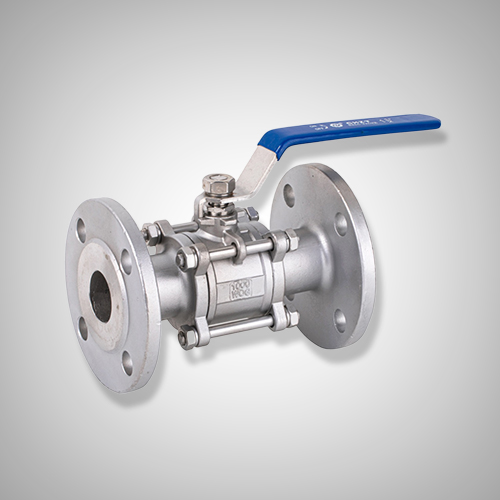
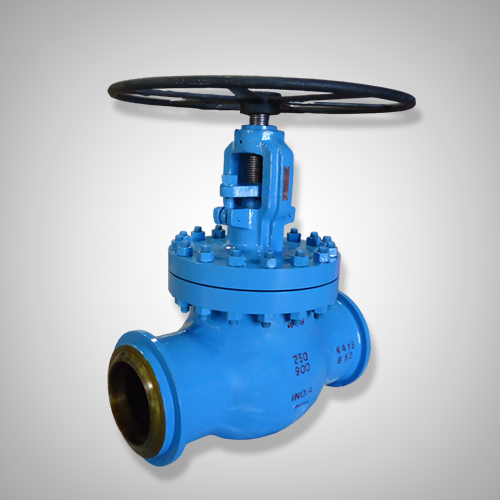
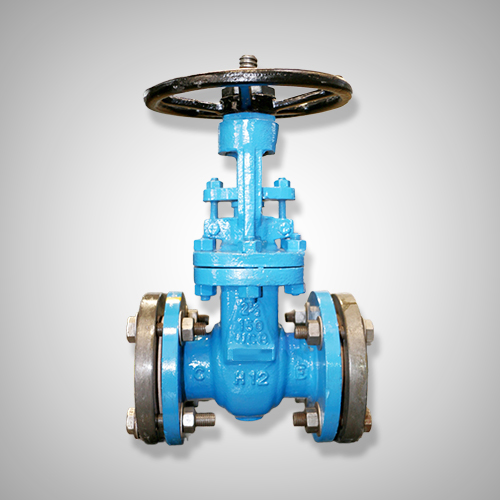
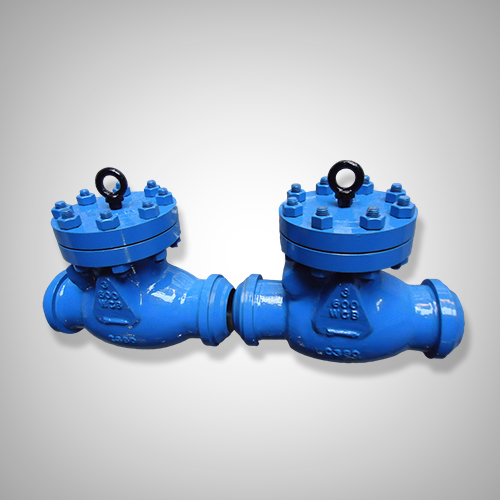
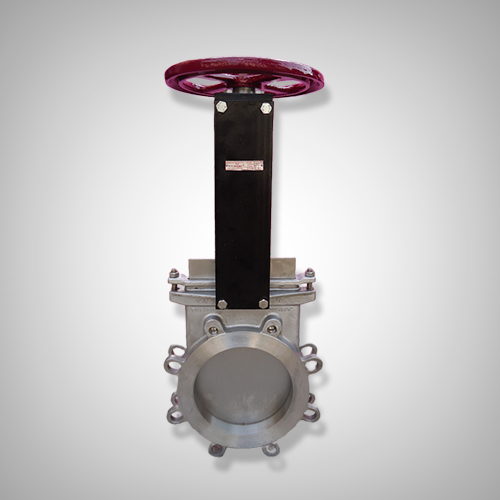
Material Selection for Oil and Gas Valves
Material compatibility is critical in oil and gas environments. We offer a wide range of cast and forged materials suitable for both sweet and sour service, offshore and onshore conditions:
- Carbon Steel (WCB, A105) : Ideal for high-pressure general-purpose flow control
- Stainless Steel (SS316, CF8M) : Excellent corrosion resistance for refineries and process systems
- Duplex Stainless Steel (UNS S31803) : High strength with resistance to chloride stress corrosion
- Super Duplex Stainless Steel (UNS S32750, S32760) : Exceptional performance in sour gas and offshore environments
- Alloy Steels and Special Grades : Available for NACE MR0175 / ISO 15156 compliance
Every valve can be supplied with test certificates, material traceability reports, and compliance documentation to meet project specifications and international standards.
Why Choose Phoenix ValSteer for Oil and Gas Valves?
- Trusted Engineering Legacy : Over 40 years of experience in high-pressure valve design and manufacturing
- Sour Service Ready : NACE-compliant materials and construction for H₂S-rich environments
- Project-Ready Lead Times : Fast delivery for shutdowns, expansions, and urgent replacement needs
- Full Quality Assurance : 100 percent hydro-tested valves with third-party inspection available
- Custom Manufacturing : Tailor-made valves for unique flow media, actuation needs, and space constraints
Ready for Your Next Oil and Gas Project?
Our valves are already working under pressure across some of the most challenging oilfields, rigs, and refineries. We can support you from inquiry to installation with fast, reliable service and valves that are built to last.