In the pulp and paper industry, flow is anything but clean water. From wood chips and pulp slurry to bleaching chemicals and steam, the media is abrasive, corrosive, and tough on valves. Downtime means lost productivity and waste buildup. That’s why Phoenix ValSteer builds valves engineered for the harshest pulp and paper processing conditions.
Whether you’re managing black liquor recovery or high-temperature steam, our valves are trusted to isolate, regulate, and protect the flow — even when the pipeline is packed with fiber and solids.
What the Pulp and Paper Industry Needs from Its Valves
Pulp and paper plants convert raw biomass into paper and packaging materials through processes like pulping, bleaching, washing, drying, and chemical recovery. These systems demand valves that can withstand fiber-laden slurries, high-cycle operations, corrosive chemicals, and fluctuating pressure or temperature conditions — all while maintaining reliability and tight shut-off.
Common Challenges in Paper Mill Valve Applications
- Handling pulp slurry and fibrous solids without clogging or wear
- Resistance to chemicals like caustic soda, chlorine dioxide, and black liquor
- Erosion and scaling inside the valve body and seat
- Maintaining seal integrity under steam and condensate conditions
- Long service life under high cycle and abrasive flow
- Minimal downtime during valve replacement or repair
Where Our Valves Are Used in Pulp and Paper Plants
Our valves are operating in kraft mills, tissue plants, and integrated paper factories across key stages:
- Pulping and digester systems : Knife gate valves for thick fiber slurries
- Washing and bleaching stages : Globe and ball valves for chemical injection and control
- Steam and condensate loops : Gate and globe valves for high-temperature lines
- Black liquor handling : Corrosion-resistant check and knife gate valves
- Effluent and wastewater : Slurry-grade valves for sediment and sludge lines
Recommended Valve Types and Pressure Classes
Valve Type | Pressure Class Range | Common Materials | Typical Application |
Knife Gate Valve | Class 150 to 300 | SS316, CF8M, Duplex | Slurry and pulp line isolation |
Gate Valve | Class 150 to 600 | WCB, SS304, SS316 | Steam and general service |
Globe Valve | Class 150 to 600 | SS316, CF8M | Chemical dosing and temperature control |
Ball Valve | Class 150 to 600 | PTFE-lined, SS316 | On-off flow of corrosive bleaching agents |
Check Valve | Class 150 to 300 | CF8M, Duplex | Black liquor and chemical recovery loops |
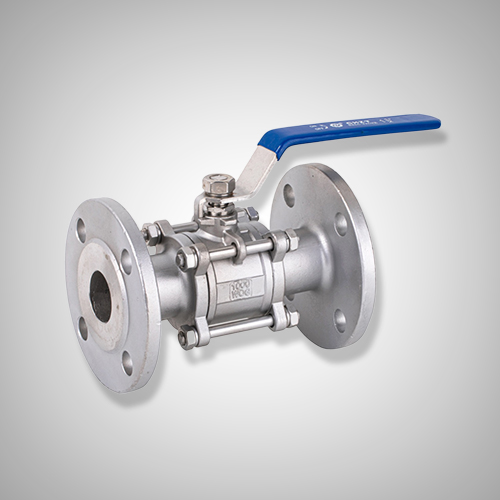
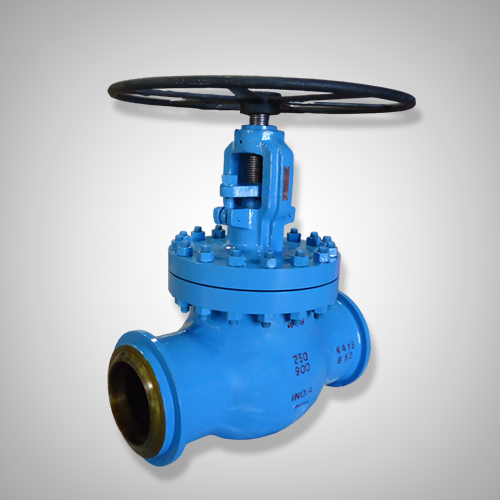
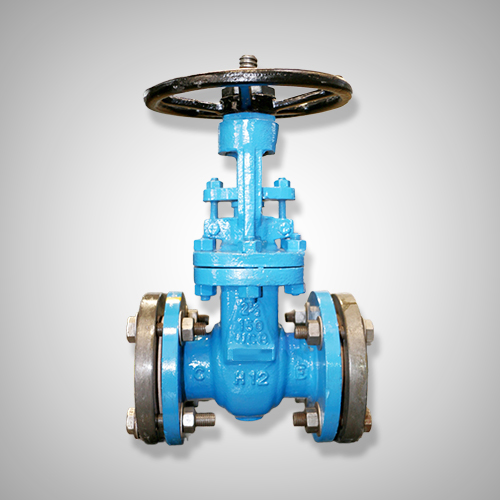
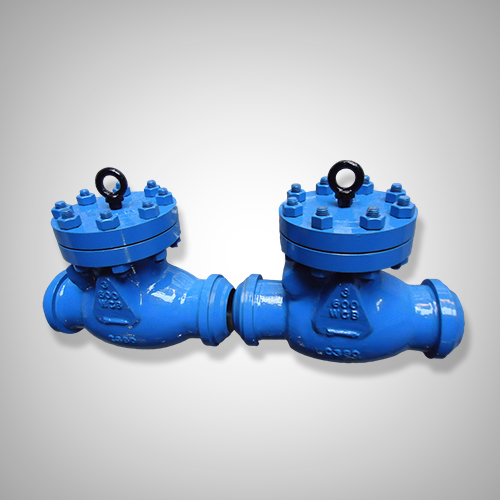
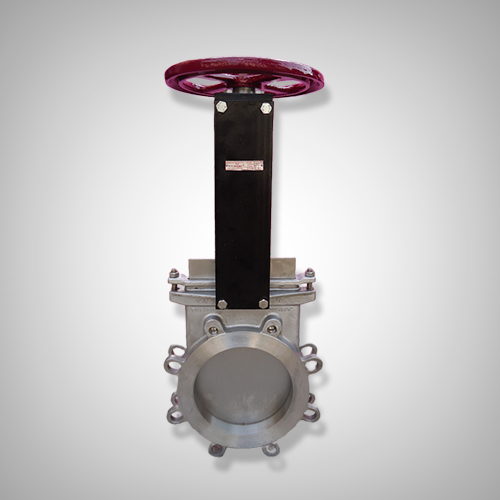
Materials We Use for Pulp and Paper Valves
Our valves are constructed from materials that perform reliably in fiber-rich, chemical-laden, and thermally dynamic environments:
- SS316 / CF8M : Corrosion resistance against bleaching agents and caustics
- Duplex Steel : High strength and erosion resistance in slurry-heavy lines
- WCB / Carbon Steel : Economical for steam and utility lines
- PTFE-lining : For highly corrosive media such as chlorine dioxide
- Available with solid wedges, hard-faced trims, and full traceability for process-critical areas
Why Choose Phoenix ValSteer for Pulp and Paper Valves?
- Slurry-Ready Designs : Our knife gate valves are made to pass fiber without clogging
- Cycle-Tested Reliability : High-performance sealing in valves designed for repeat use
- Fast Replacement, Minimal Downtime : Compact designs and available spares reduce shutdown windows
- Corrosion and Erosion Resistance : Valves tailored to black liquor, bleach, and pulp applications
- Custom Manufacturing : Optional actuator mounting, custom face-to-face, and special port designs
Want Valves That Keep Your Pulp Flowing Smoothly?
Whether it’s virgin pulp, recycled paper, or chemical recovery, Phoenix ValSteer valves are built to handle it all — thick fluids, high temperatures, and aggressive chemicals. Speak to us about selecting the right valve for each stage of your paper production line.