In power plants, the margin for error is razor-thin. Whether it’s a fossil fuel station, a nuclear facility, or a renewable power installation, the valves used in power generation must withstand extreme pressure, thermal shock, and demanding operating cycles — all while delivering precision control and absolute reliability.
At Phoenix ValSteer, we manufacture industrial valves that power up when others burn out. From boiler feed isolation to steam control and condensate return, our valves are engineered for performance and safety in high-pressure, high-temperature environments.
What the Power Industry Needs from Its Valves
Power generation plants operate under continuous load, often in harsh, high-temperature conditions. Whether handling steam, water, gas, or chemicals, valves must control flow accurately and survive thermal cycling, scaling, and erosive wear. A valve that sticks, leaks, or fails can lead to unscheduled shutdowns, safety hazards, and huge financial losses.
Common Challenges in Power Plant Valve Applications
- Extreme pressure and temperature fluctuations (HPHT)
- Thermal cycling and steam flashing that cause metal fatigue
- Erosion from high-velocity water and steam flow
- Corrosion from demineralized and chemically treated water
- Tight shut-off requirements for safety and performance
- Continuous-duty cycles with low tolerance for downtime
Where Our Valves Are Used in Power Plants
Phoenix ValSteer valves are trusted by thermal, hydroelectric, nuclear, and combined-cycle power plants across key flow control points:
- Boiler feedwater systems – High-pressure gate and globe valves
- Main steam lines – Globe and ball valves in alloy and forged bodies
- Condensate return systems – Check valves to prevent backflow into turbines
- Cooling water circuits – Butterfly and gate valves in SS and DI
- Chemical dosing –PTFE-lined valves for pH control and demineralization
Recommended Valve Types and Pressure Classes
Valve Type | Pressure Class Range | Common Materials | Typical Application |
Gate Valve | Class 600 to 2500 | WCB, A105, F22, CF8M | Isolation in boiler feed and main steam systems |
Globe Valve | Class 600 to 1500 | CF8M, Alloy Steel, F11, F22 | Steam throttling and pressure control |
Ball Valve | Class 150 to 1500 | A105, CF8M, Forged Steel | On-off service in auxiliary and condensate lines |
Check Valve | Class 150 to 1500 | CF8M, Super Duplex | Turbine protection and condensate return |
Butterfly Valve | Class 150 to 300 | DI, SS316, Epoxy-Coated CI | Cooling water and service lines |
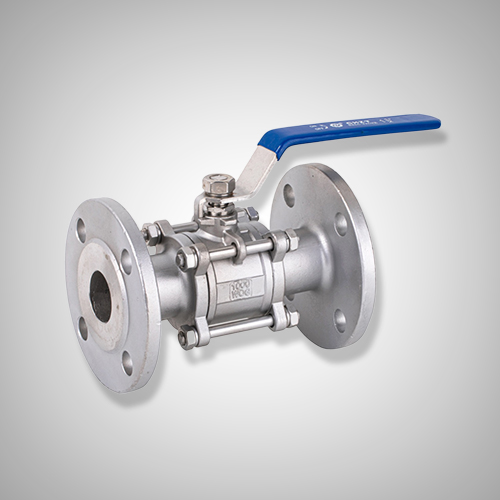
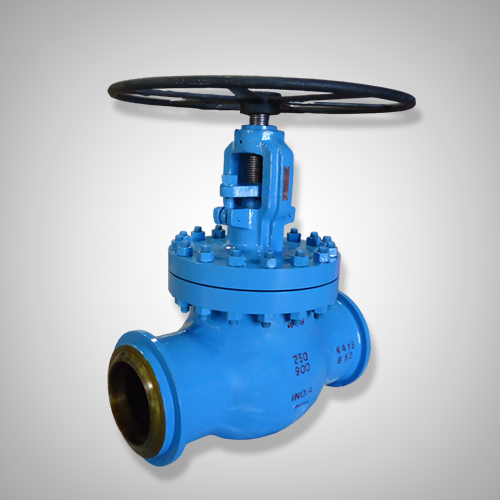
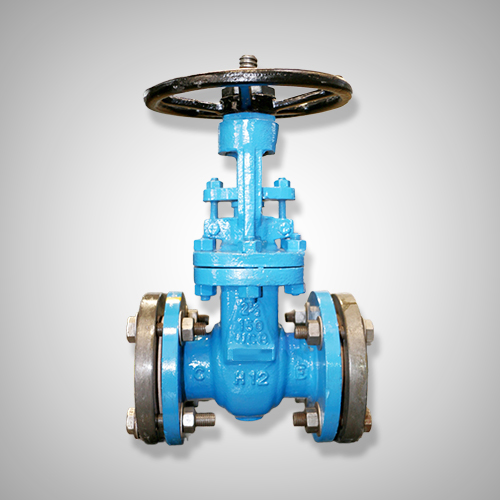
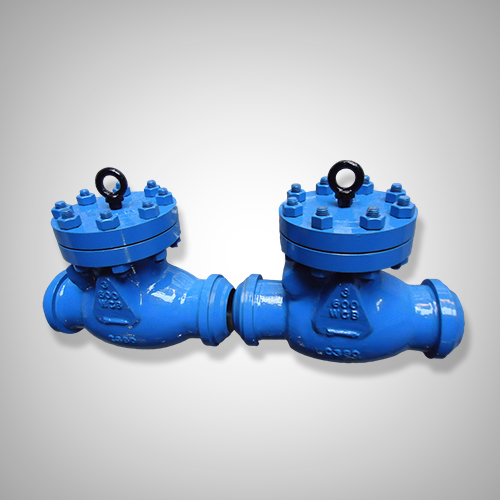
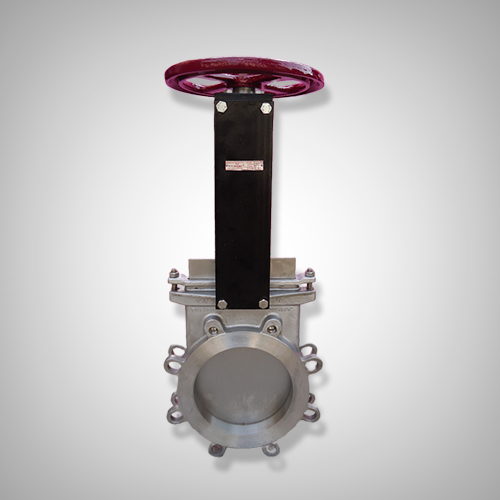
Material Selection for Power Generation Valves
The operating conditions in power plants demand carefully selected materials that can handle high temperatures, corrosion, and erosion. Phoenix ValSteer offers:
- Carbon Steel (WCB, A105) : Suitable for high-pressure, moderate-temperature lines
- Alloy Steels (F11, F22, F91) : High-temperature resistance in steam systems
- Stainless Steel (SS316, CF8M) : Ideal for corrosive condensate and chemical dosing
- Super Duplex : Used in seawater-cooled power stations and aggressive water chemistry
- Forged Bodies : Available for critical applications with compact design requirements
All materials can be supplied with third-party inspection, hydro test reports, and compliance to ASME, API, and PED standards.
Why Choose Phoenix ValSteer for Power Plant Valves?
- Built for Pressure and Heat : Our valves are pressure-tested and thermally engineered for long service life
- Forged and Cast Options : Available based on size, pressure, and dimensional constraints
- Application-Specific Designs : We recommend the right valve and material for every point in your flow diagram
- Fast Project Turnaround : Rapid support for shutdowns, expansions, and new builds
- Global Standards, Local Service : Fully compliant with international norms and responsive support teams
Keep Your Power Plant Flowing with Confidence
From start-up to shutdown, your power plant needs valves that can take the heat and hold the pressure. Phoenix ValSteer delivers precision-built, performance-tested valves that meet the exacting demands of today’s energy infrastructure.